Research & Development Equipment of the Pipe, Tube and Bar Steel Technology Center
The Pipe, Tube and Bar Steel Technology Center is equipped with dedicated equipment for research, development and testing of pipe, tube and bar steel products. It has equipment for sample preparation, metallographic phase and hardness testing, tubing and casing thread machining, physical performance, hydrogen sulfide and carbon dioxide corrosion, fatigue of wire rod and cold heading. It can conduct metallographic phase and hardness tests on materials, full-size physical performance tests on steel pipes and tubes, collapse resistance tests on tubing and casing, hydrogen sulfide stress tests, and carbon dioxide corrosion tests. It can also conduct performance tests regarding fatigue, torque and cold heading of wire rod products for auto parts.
-
Sample Preparation
Laboratory -
Physical Testing
Laboratory -
Tubing and Casing
Processing and Testing Center -
Hydrogen Sulfide
Corrosion Laboratory -
Bar and Wire Rod
Performance
Testing Laboratory
With autoclave test equipment manufactured by well-known American and Chinese companies for simulating actual working conditions of products, it can provide methods A, B, C and D in conformity with the requirements of NACE. It also has testing equipment such as stress rings and constant-temperature soaking tanks, which is used for conducting tests such as four-point bending and HIC.
- Slow strain rate test (SSRT) machine
- Autoclave Testing Machine
- Constant strain stress corrosion testing machine
- Soaking tank test equipment
Slow strain rate test (SSRT) machine
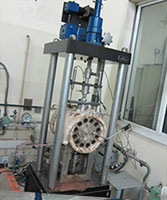
Testing equipment used for performance tests of connectors of tubing and casing for oil and gas exploitation and production as well as for mechanical behavior studies of tubing/casing strings. In conformity with the requirements of standards such as ISO 13679 and API RP 5C5, it can perform applicability assessment tests on the basis of the actual oilfield and gasfield working conditions of users. Maximum axial tensile force: 15000Kn; maximum axial compressive force: 11250kN; maximum bending load: 542kN¡¤m; with a total of 15 modes including stretching, compression, bending, internal pressure, external pressure, high temperature, and combined load.
Autoclave testing machine
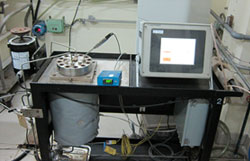
It can simulate working conditions of H2S, C02, Cl- and other media and perform tests and assessments concerning four-point bending, three-point bending, C-ring, HIC, cantilever, static corrosion, dynamic corrosion and other aspects of products. Maximum temperature: 350 ¡æ; maximum pressure: 35MPa; maximum flow rate: 4.5m/s; volume: 5, 7.5, and 10 liters.
Electrochemical test system
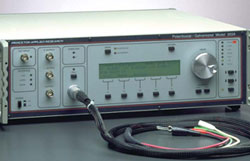
Provided by Princeton Applied Research, this system can be used in connection with the high-temperature autoclave for electrochemical in-situ measurement via simulation of actual working conditions of oil and gas fields.
Constant strain stress corrosion testing machine
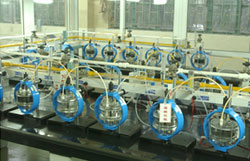
It can be used for product testing in accordance with Method A specified in NACE TM0177. Temperature: 24 ¡æ ¡À 3 ¡æ; pressure: 0.1MPa.
Soaking tank test equipment
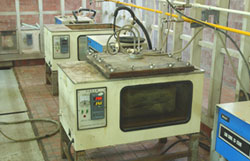
t can be used for product testing in accordance with Method C, Method B and Method D specified in NACE TM0177 and four-point bending and HIC specified in NACE. Temperature: 24 ¡æ ¡À 3 ¡æ; pressure: 0.1MPa